摘要:以某汽车模内转印(IMD)内饰面板为研究对象,建立了基于Moldflflow的内饰板仿真模型。通过Box-Behnken Design(BBD)试验和响应曲面法分析翘曲变形的影响因素,建立了翘曲变形与各工艺参数值之间的映射关系。利用粒子群优化算法(PSO)对响应曲面模型进行全局寻优,求解得出最优工艺参数组合及所预测的最小翘曲变形值。按照最优工艺参数值进行模拟,验证算法的准确性。最后通过实际注塑成型与翘曲变形测量实验,验证仿真优化结果与实际变形趋势的一致性。
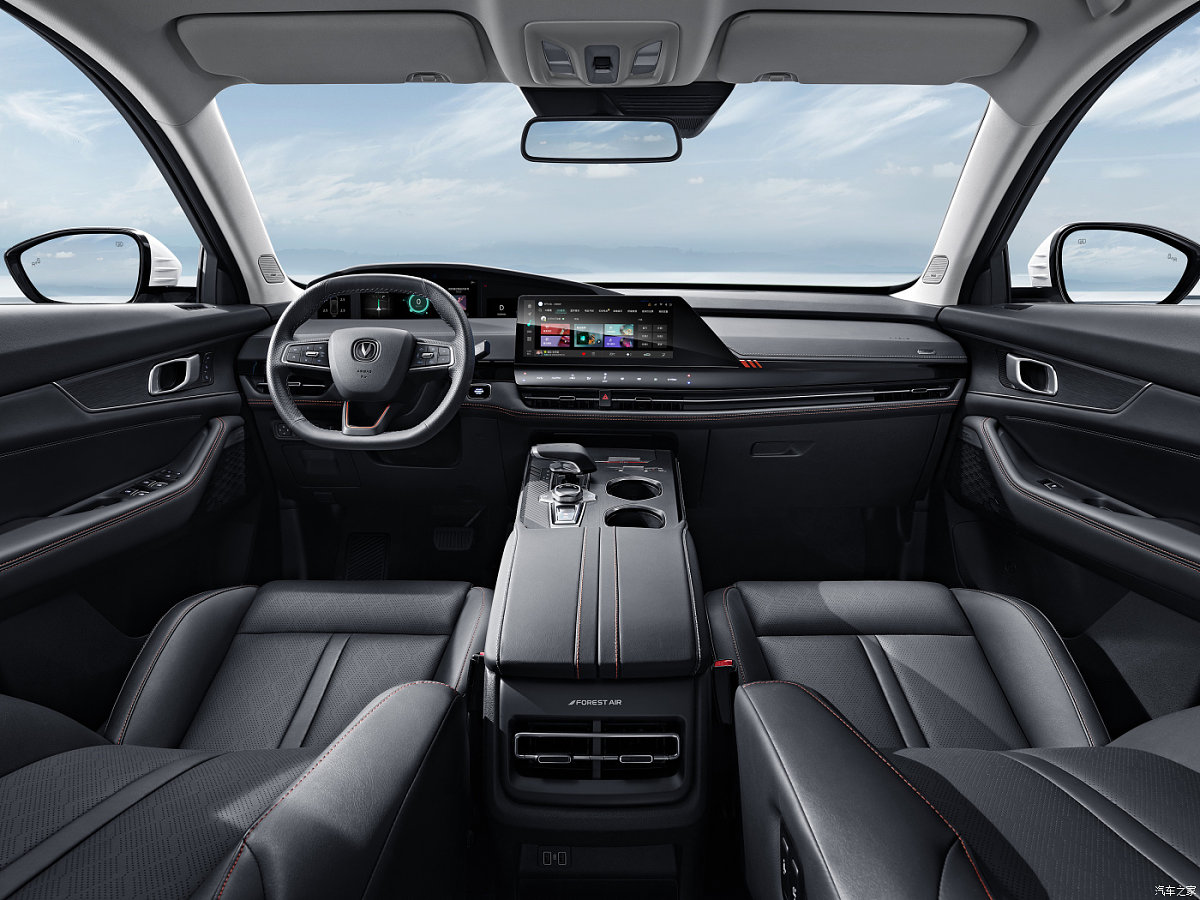
模内转印(IMD)是一种可同步完成部件注塑和产品表面装饰的模内装饰技术,其可使产品集装饰性与功能性于一体,是一项生产效率高、产品成本低的技术[1]。自上世纪80年代由日本写真印刷株式会社将IMD技术推广应用至今,经过30多年的不断发展,IMD技术凭借其生产成本低、经久耐用及环保的优势,正在逐步取代传统的模后涂漆、水转印、热冲压和镀铬等工艺。IMD工艺首先在电子家电以及手提电话等中等尺寸的塑件中获得成功应用。目前IMD技术已广泛应用于汽车内外饰的大型塑件中,如汽车的整体仪表盘、保险杠、门板等。
IMD技术虽然具有许多传统装饰工艺所不具备的优势,但其对成型工艺的要求较高,尤其是对于具有复杂形状的汽车内饰件,在成型过程中如果对工艺调整不当,很容易出现产品质量缺陷[2]。塑件的翘曲变形就是其中一个重要问题,虽然普通注塑产品也会出现同样的问题,但由于IMD技术是将塑料薄膜和熔体在型腔内一体固化成型,在冷却时薄膜的滞热作用会使塑件冷却不均的程度加大,翘曲问题相比于普通塑件会更加严重[3-5]。因此减小覆膜制品的翘曲变形非常关键[6]。
目前汽车塑件的注塑成型工艺分析主要集中在传统塑件上,关于IMD技术的工艺过程分析国内文献很少报道。本文使用Moldflflow软件模拟某汽车IMD内饰板的注塑过程,基于试验设计以及响应曲面法建立翘曲变形响应曲面模型,并利用粒子群优化算法 (PSO)求解最优工艺参数组合,最后通过仿真与实验验证优化方法的准确性。
IMD内饰板仿真模型建立
本文选择某汽车副仪表盘的右装饰面板,IMD内饰板模型如图1所示,该内饰板尺寸928 mm×147 mm×85 mm,基本壁厚3 mm。内饰板表面为不规则的曲面,且含有沟槽与圆角等特征,圆角角度较为平缓,造型特点适合于IMD工艺,曲面落差与圆角大小均在装饰薄膜拉伸范围内;内饰板背面分布若干装配锁扣、加强筋、扣位以及BOSS柱等装配和增强结构。
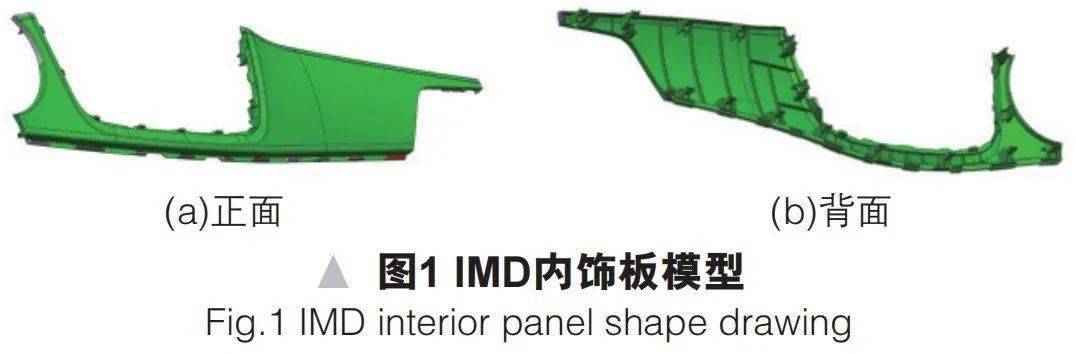
将产品CAD数据导入Moldflflow中划分网格。产品造型狭长,又是薄壁结构,因此仿真模型采用中性面网格划分,对划分完毕的模型经过成型窗口分析以及浇口分析、充填分析等,分别为模型设置合适的浇注系统。由于注塑成型时产品正面包覆厚度0.125 mm的装饰薄膜,薄膜的滞热作用会在产品冷却时延缓散热而导致冷却不均,因此设置冷却系统时应考虑加强动模侧的散热。设置冷却结构为随形冷却,并将动模侧冷却水道与塑件距离设置为15 mm,定模侧为30 mm,内饰板以及浇注系统和冷却系统的仿真模型如图2所示。
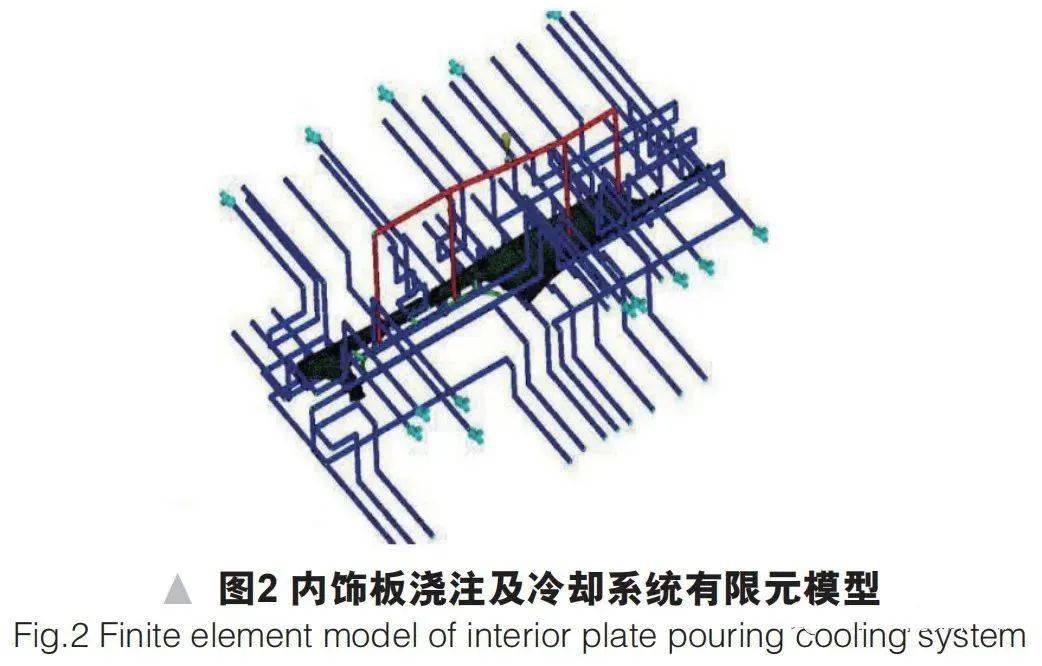
内饰板所用材料为聚碳酸酯/丙烯腈-丁二烯-苯乙烯共聚物 (PC/ABS)合 金,牌号为DSPCASB-01。该材料结合PC和ABS两种材料的优异特性,具备良好的成型性、力学性能和耐温、抗紫外线等特性,已广泛用于汽车内饰件中。仿真模型首先按照材料推荐的工艺参数设置,仿真得到的最大翘曲变形量为9.35 mm,翘曲变形较大处集中于内饰板的末端狭长部位,如图3所示。因此需采用合适的试验设计方法调节工艺参数,以降低最大翘曲变形量。
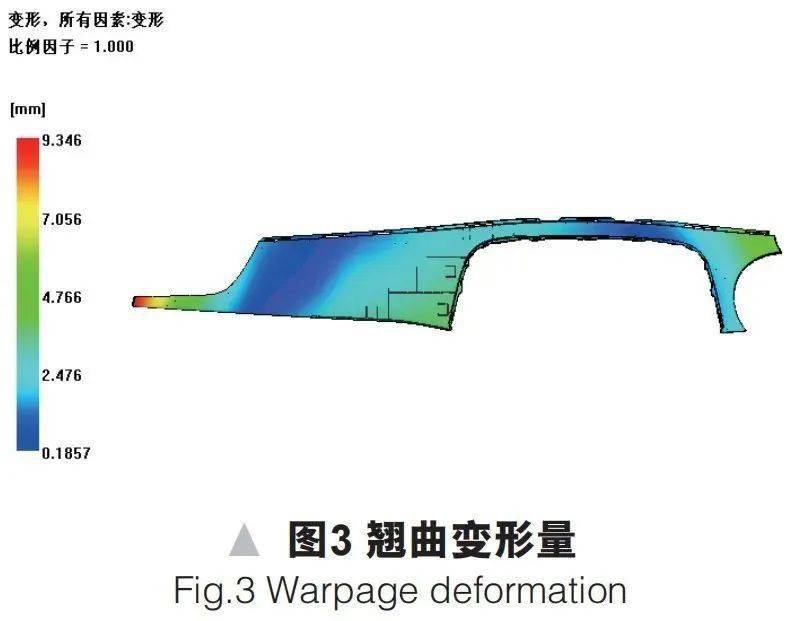
BBD试验设计
试验设计方法是将数学统计领域中的优化理论应用到科学实验中,可以更有序地设计试验;该方法是整理数据的方法,同时也是节省时间成本、 降低实验费用的高效方法[7]。常用的试验设计法有BBD设计 (Box-Behnken Design)、田口正交设计、中心组合设计、均匀设计等[8]。本文采用BBD试验设计法为响应曲面提供数据样本,建立响应曲面方程,分析各参数对IMD内饰件翘曲变形的影响。并利用粒子群优化算法 (PSO)对数学模型进行优化,寻找使翘曲变形最小的工艺参数最优组合。
选取翘曲变形量作为试验设计的优化目标。参考工程研究经验,影响塑料产品翘曲变形的工艺参数 (因素)主要有模具温度 (A)、熔体温度 (B)、保压压力 (C)和保压时间 (D),故选取上述4个因素作为设计变量。根据生产商提供的材料推荐工艺范围,将优化目标与设计变量按照BBD设计设置4因素3水平试验表,如表1所示。由于内饰板使用0.125 mm薄膜,其滞热作用将对成型质量产生影响,因此应设置不对称模具温度,即定模温度比动模温度高 20℃,以减少薄膜滞热产生的冷却不均现象。
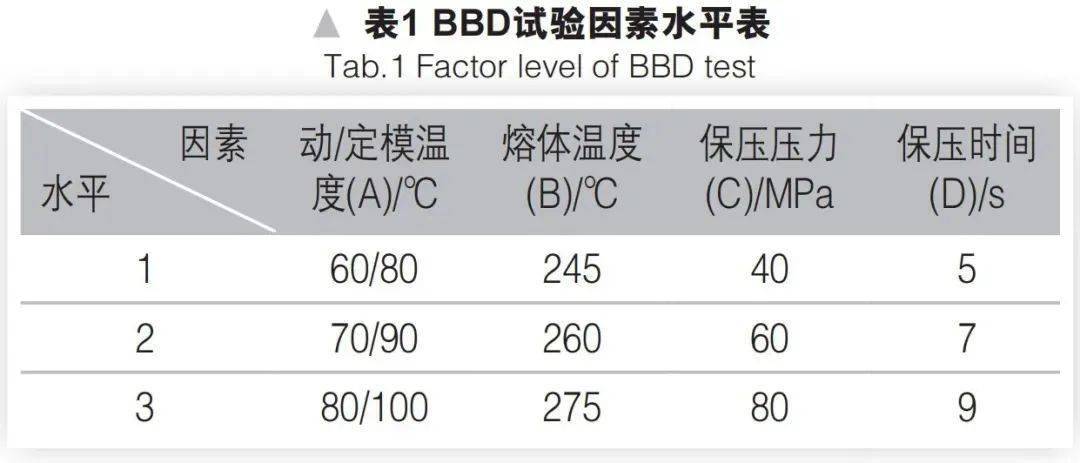
试验结果与分析
试验结果
根据表1的因素水平可得到如表2所示的29组试验,将各组设计变量导入Moldflflow中得到优化目标翘曲变形量的仿真结果。
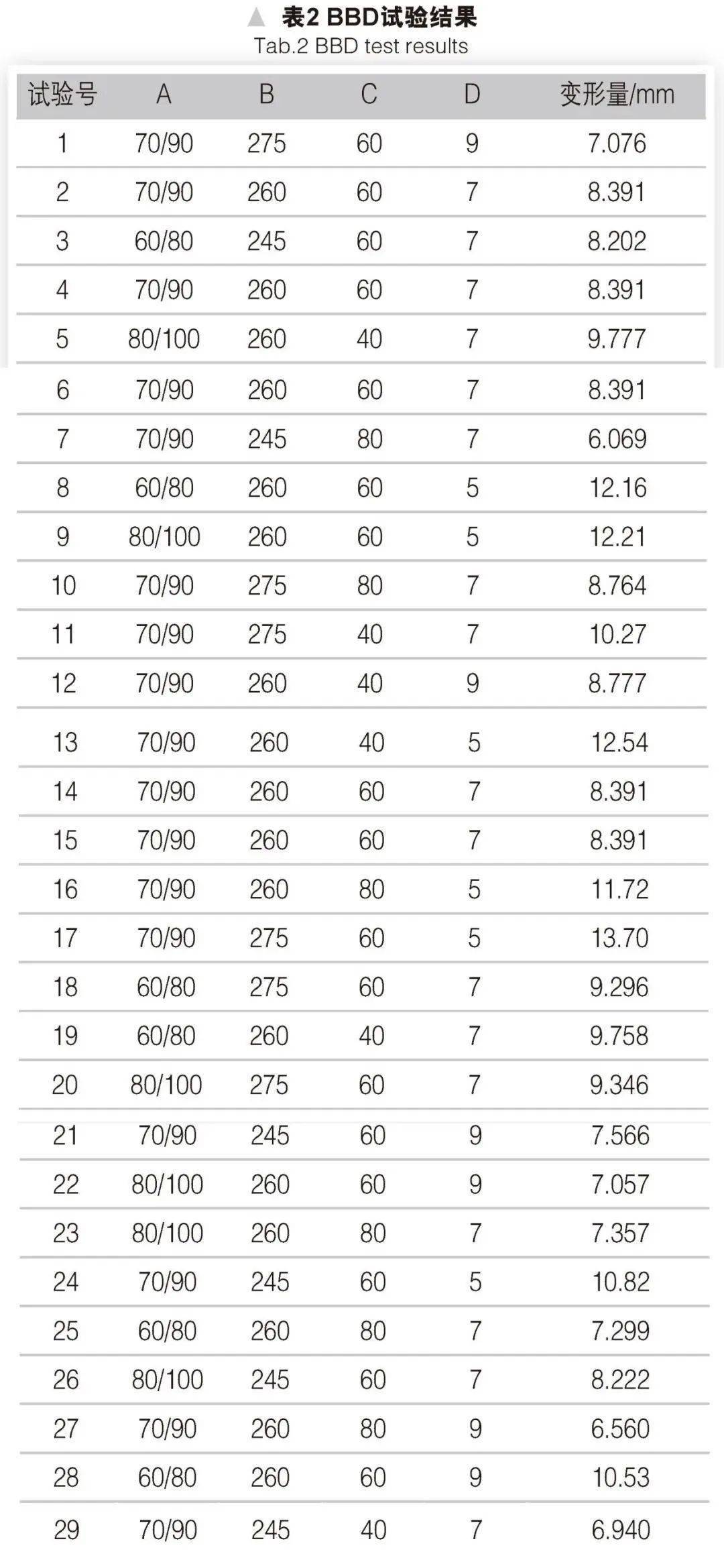
从表2可以看出,基于BBD设计方法的4因素3水平试验数为29,虽然试验次数较多,但相比于正交试验点的不连续性,其优势在于通过试验点可以进行后续的连续性分析,从而建立起优化目标对于设计变量之间的响应方程,使整个优化模型更为精确。根据Moldflflow仿真结果可以看出,第7组试验的翘曲变形量最小(6.069 mm)。
方差分析与响应面模型的建立
为了进一步研究各因素对翘曲变形量的影响程度,需对试验结果进行方差分析。方差分析可以准确显示不同条件下试验结果的数据波动,判断所考察因素的影响程度是否显著[9]。本次试验方差分析采用多元二次模型,经过计算,得出翘曲变形的方差分析结果如表3所示。

从表3可以看出,整个模型的P值小于0.0001, 说明试验数据在统计学上是有意义的,只有0.01%的概率产生噪声,模型可以有效地拟合数据。影响翘曲变形的因素按显著度大小顺序依次为保压时间、熔体温度、保压压力、模具温度,即D>B>C> A。其中D、B与C的P值均小于0.01,影响极其显著;而模具温度A的P值大于0.05,对优化目标的影响较小,说明不对称模具温度消除了薄膜滞热带来的冷却不均的影响,从而降低了厚度方向的翘曲,对成型质量的影响低于其他参数。
模型响应值的变异系数CV值为8.29%,较低的数值说明试验结果是可信的。根据最小二乘法原理对试验数据拟合后可得模型的二阶方程式(1)。
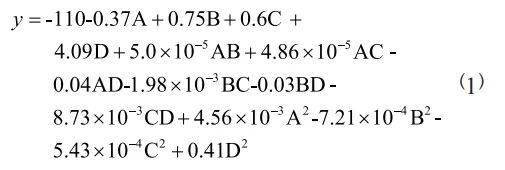
对回归方程进行残差分析,可得到残差图,如图4所示。
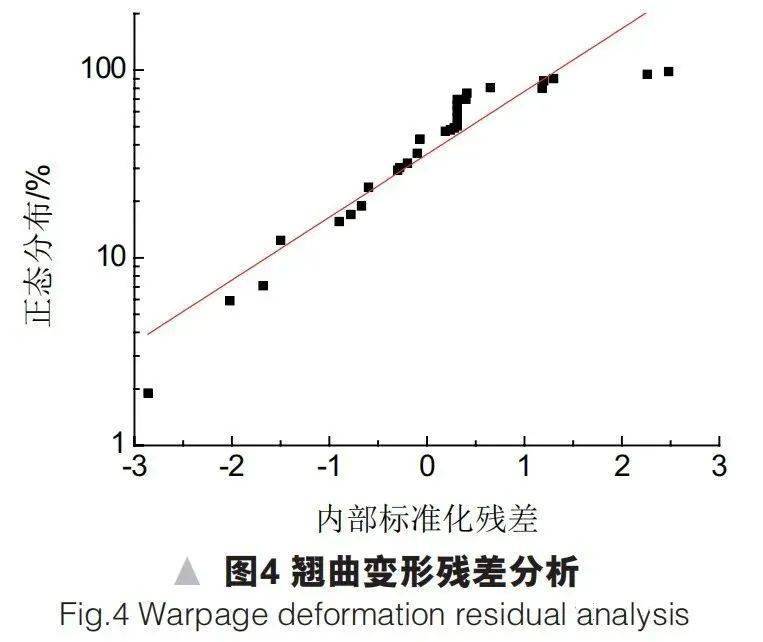
图4中,横坐标为标准化后的残差,纵坐标为正态分布概率,图中大部分响应变量残差与预测值保持一致,仅有少量值分布于拟合直线两侧,表明误差呈正态分布,数学模型对试验数据的拟合较好。
粒子群算法寻优与仿真验证
粒子群优化算法PSO是在模仿鸟群捕食行为 的基础上逐渐发展起来的一种群体相互合作的随 机搜寻算法[10]。经过多年的发展与改进,该算法在 求解多目标非线性耦合问题、多峰极值问题等方面 可提供快速、高效的求解算法,目前在多领域的工 程优化中受到越来越多的关注。本文的优化问题 用数学方法表示,即多元函数的极值求解问题,式(1)中的函数f(y)是关于翘曲变形的多元二次回归方 程,目标是寻找一组解使f(y)取得最小值。
设定PSO算法中粒子群数目为10,最大迭代次数Gmax为100次,惯性权重w为0.9,粒子增量为0.9。在粒子的迭代更替中,全局最优值gbest由当前粒子pbest的平均值得出,粒子每次迭代后的位置更新也由粒子自身飞行位置的最优值Pi与整体粒子最优 值Pg共同作用产生。在经过49次迭代后,优化算法得出最优工艺参数组合,此时的极值为5.18mm,相应的坐标为(69.37/89.37、264.32、80.0、8.70),即动模温度设定为69℃,定模温度89℃,熔体温度设定为 264.32℃,保压压力80MPa,保压时间取8.7 s。为了初步验证算法的可靠性,在Moldflflow中按照最优工艺参数组合对IMD内饰面板进行仿真,得到翘曲变形最大值为5.507 mm,如图5所示。对比PSO算法搜索的最佳参数组合,误差仅为5.99%,因此可以验证本文使用的优化方法是有效的。
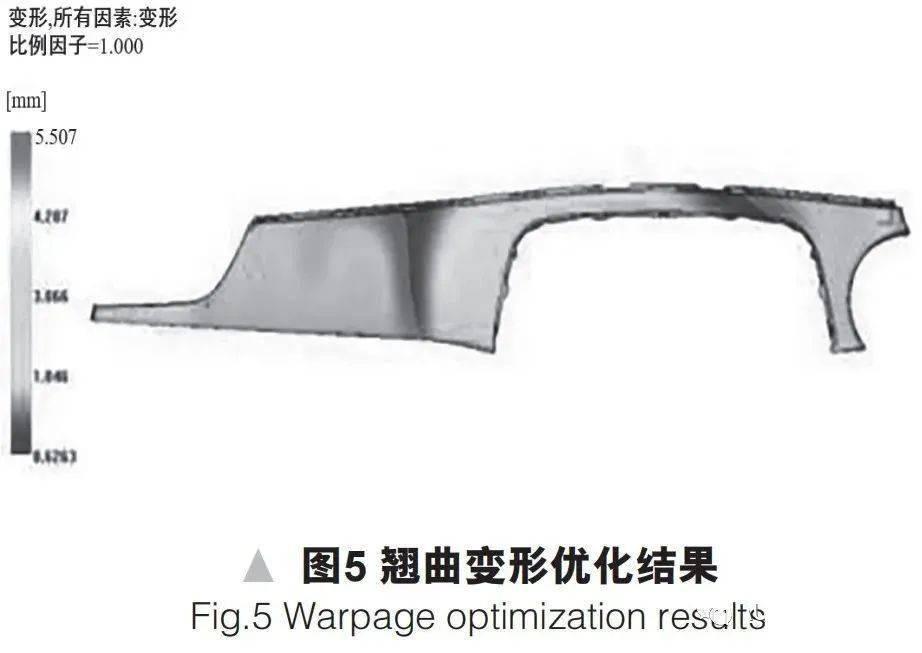
实验验证
实际样件加工
为了进一步考察本文所采用的试验设计方法 以及优化算法下的CAE仿真模拟数据的准确性,有必要设置实验来验证实际工况下,产品成型的翘曲变形是否达到最小,且是否符合工程标准。
在注射机、送膜机等基本注塑环境下,按照工艺要求制作IMD注塑模具,其中浇注系统、冷却系统等的基本结构均与CAE仿真模型保持一致。为方便薄膜由送膜机输入模具型腔,模具应采用倒装模结构,如图6所示。另外,实验中需使用与仿真相同的塑料基材、薄膜片材以及最优工艺参数组合。最后将材料与设备按照IMD注塑工序进行注塑成 型,得到的实际加工样件如图7所示。
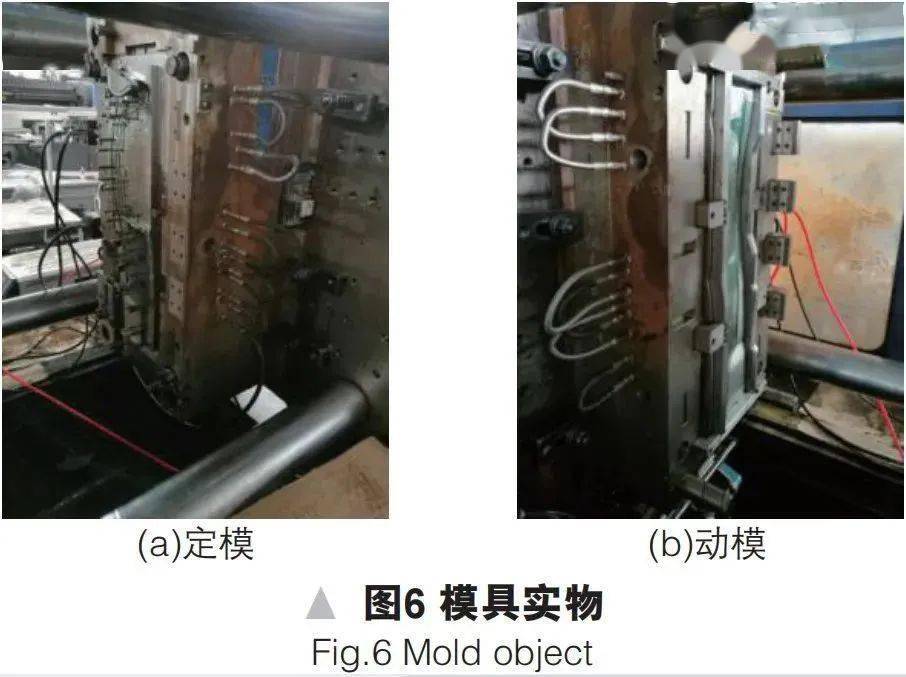
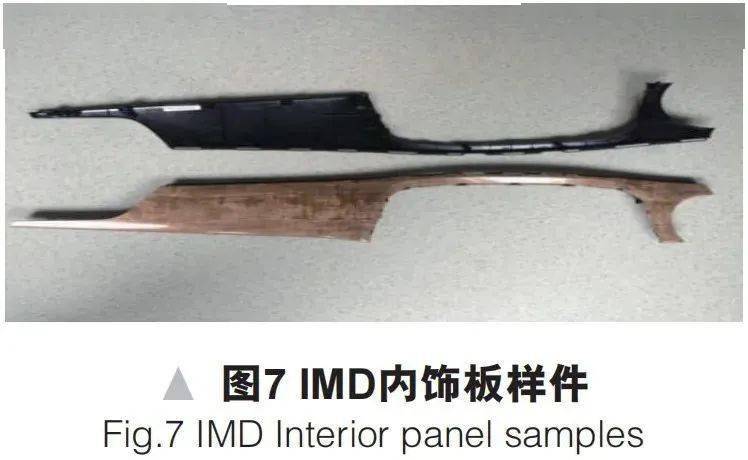
翘曲变形测量
为了准确测量IMD面板的变形趋势,需使用大型桥式测量仪对其进行精确测量,测量的基本原理是通过夹具将产品固定后,建立虚拟坐标系,利用高精度探头精密测出产品测点位置的x、y、z坐标, 并将实际测量数据与产品模型相应的测点坐标进行比对,得出位置偏差。按照该测量原理,在产品模型中易发生翘曲的边缘位置标记40个测量点用于实际测量,并记录每个点的位置坐标。将加工完成的IMD内饰板样件送入三坐标测量仪并使用夹具固定,设置内饰板数模坐标系作为测量的虚拟坐标系,且与Moldflflow中仿真模型坐标系一致。最后依次测量样件所有测点并记录测量数据,测量环境如图8所示。
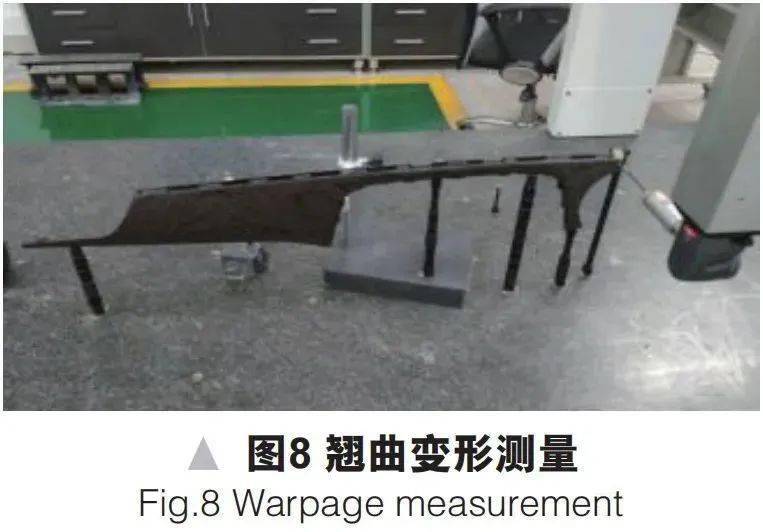
测量结果与数据分析
为进一步验证仿真结果的可靠性,利用实验测量的数据与仿真模型对应测点的翘曲变形进行比较,结果如图9、图10所示。从图9、图10可以得出每个测点位置实际变形量与模拟变形的差异。
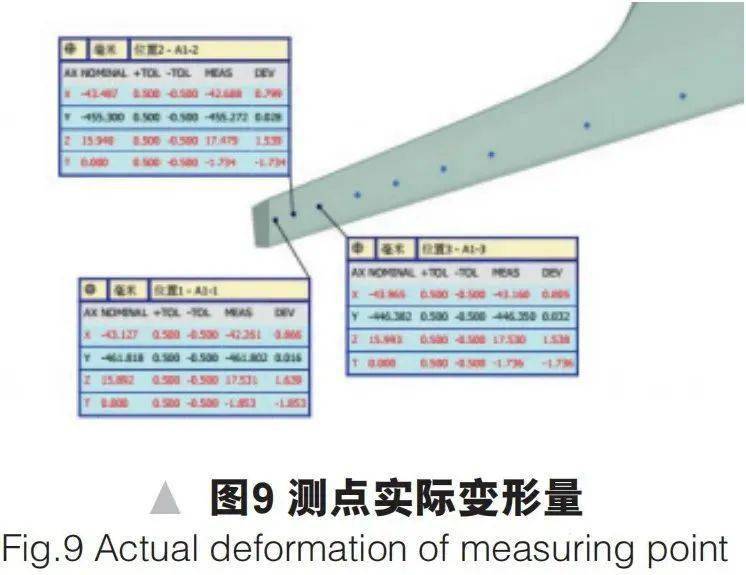
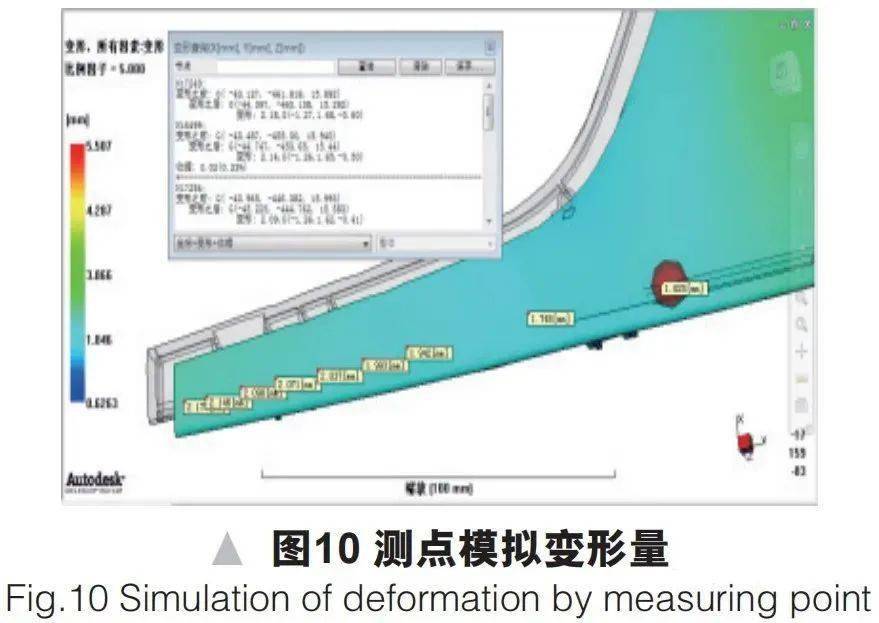
分别将样件上边缘16个测点、下边缘24个测点与其对应的模拟数据进行对比,结果如图11和图12所示。从图11、图12可以看出,实验测点数据与Moldflflow仿真模拟的数据大致吻合,其变化趋势具有良好的一致性,但是在数值上有个别数据误差较大。
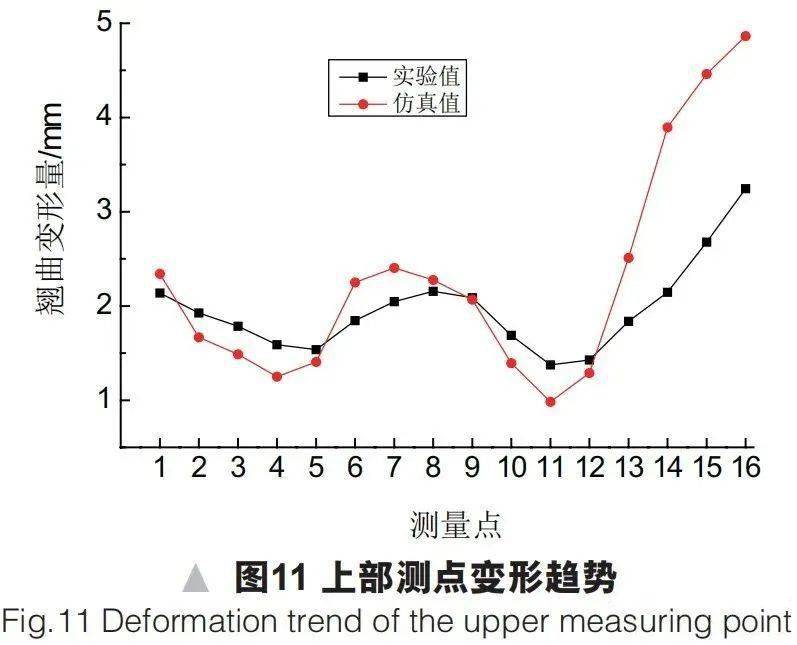
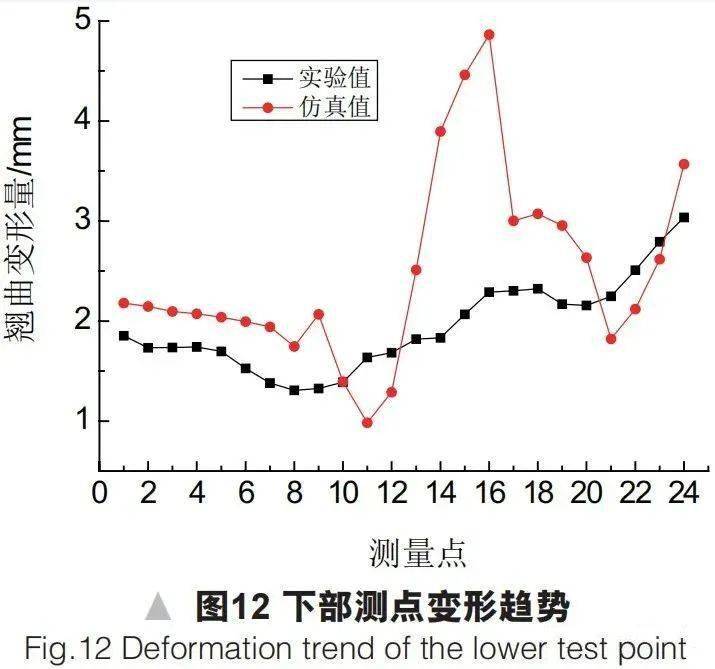
分析误差产生的原因可能是:
(1)利用三坐标测量仪定位坐标系及测量产生误差;
(2)为了提高模拟效率,降低纵横比,减少计算量,模型经过CAD Doctor前处理,对数模上部分圆角、凸台、倒角等小特征进行简化,从而在一定程度上影响了仿真精度;
(3)在Moldflflow中,由于没有模具型腔壁的限制,模型的翘曲仿真是自由变形,而实际注塑时产品变形受模具约束,同时IMD薄膜的收缩也限制了塑料基材的收缩,因此实际产品的变形量基本上低于仿真数据。
上述实验验证了本文建立的翘曲变形优化算法的可靠性以及仿真模拟的精确性,实验结果表明,优化后的产品成型质量得到了较大改善。将样件装车后检测与周围零件的配合,结果表明,测量间隙小于3 mm,面差小于0.5 mm,符合装车要求,因此证明本文对IMD副仪表盘右装饰面板翘曲变形 的工艺优化在工程上是有效的,产品装车如图13所示。
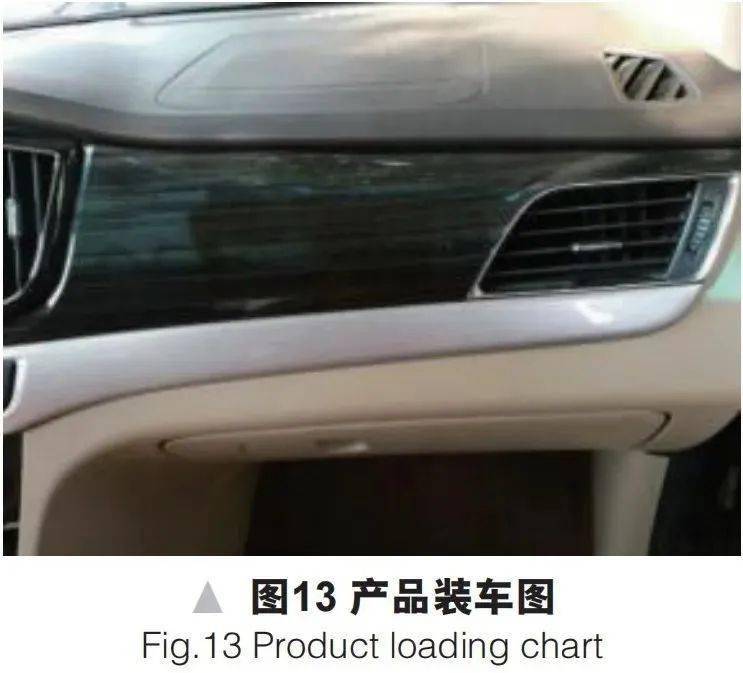
结论
(1)通过BBD试验设计以及方差分析,确定了影响IMD内饰件翘曲变形的主要因素依次为保压时间、熔体温度、保压压力、模具温度。
(2)建立翘曲变形与各工艺参数值之间的响应曲面模型,利用粒子群算法全局寻优,得出最优工艺参数组合,即动模温度设定为69℃、定模温度89℃、熔体温度设定为264.32℃、保压压力80 MPa、 保压时间取8.7 s时,具有最小的翘曲变形量5.18 mm。使用Moldflflow对优化结果进行模拟仿真验证, 验证结果与优化结果比较接近,误差仅为5.99%。
(3)通过实际注塑成型与翘曲变形测量实验,验证仿真优化结果与实际变形趋势具有良好的一致性。样件装车后检测与周围零件的配合符合装车要求,表明本文对IMD副仪表盘右装饰面板翘曲变形的工艺优化在工程上是有效的。